(home)
Over the summer of 2006 I traded my Sheldon horizontal mill for a
Bridgeport shaper head. From a money standpoint it wasn't an
advantageous trade, OTOH the shaper head fits my needs lots
better. Although the shaper head is fully functional, it lacks the
clapper box and was instead fitted with a big plain bushing. I
have heard that the clapper box design is sometimes less effective for
slotting in particular so locking or replacing them is common.
For mine, I figured I needed to make some HSS toolholders. I had
a seemingly clever idea to cut the recess for the tool, rotated by 45
degrees so the clamp would work over a corner of the bit instead of the
flat.
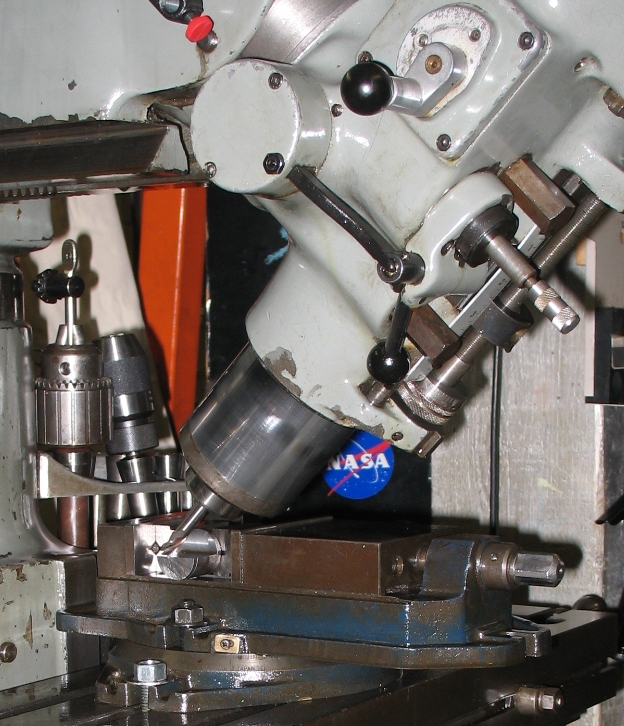
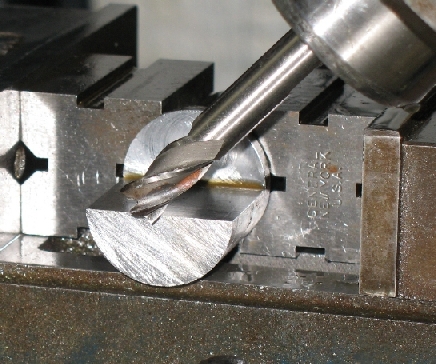
Makes for a fun picture but getting the correct rotations is subtler
than it looks. I ended up milling out the 45 degree rotation and
clamping against the flat. So much for being clever... ;)
This is the end of the shaper head ram, the clapper box and in this
case, the bushing secures here.
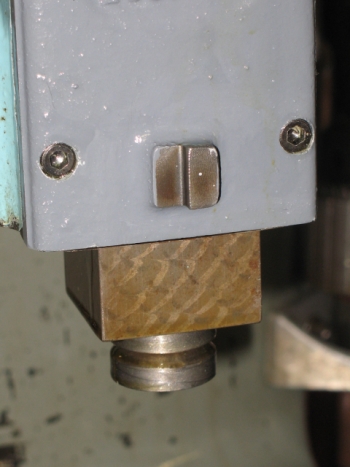
This is a view of the bushing my head came with, my homebrew toolholder
and a 3/16" HSS cutting tool with a 1/4" tool soldered to it, intended
to stiffen the otherwise very flexible cutter.
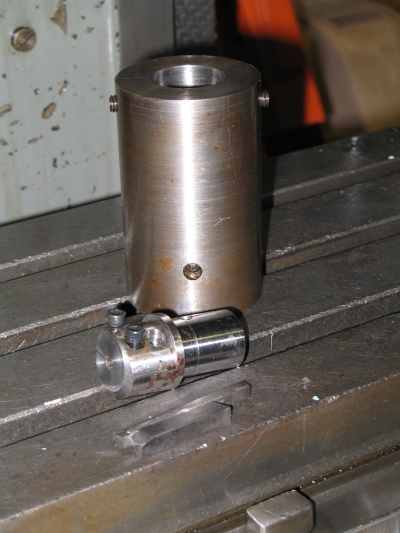
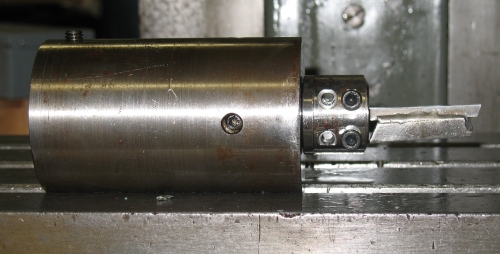
This was the first job, putting keyways into replacement gears for my
lathe. Step 1 was to bore out the 1/2" hole to 1.5". As can be
seen in the bore, I kind of messed up the finish- forgot to move up to
the 1" boring bar once so had some chatter on the final pass.
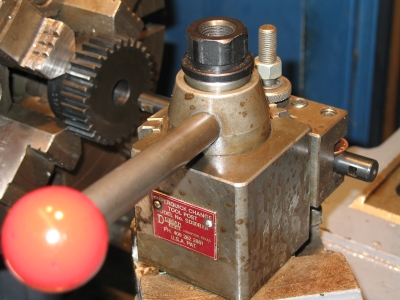
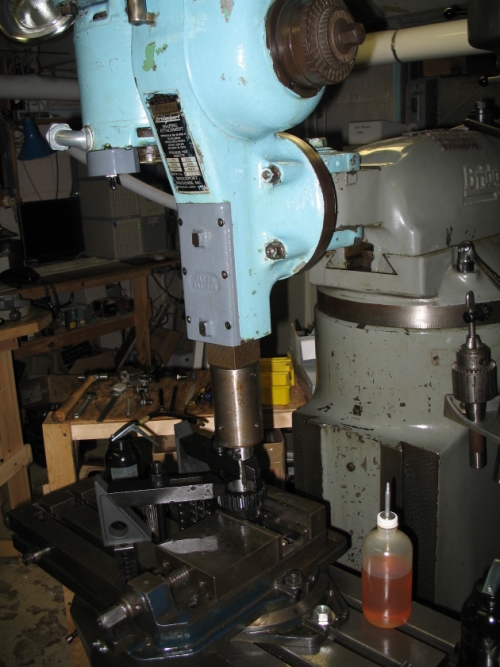
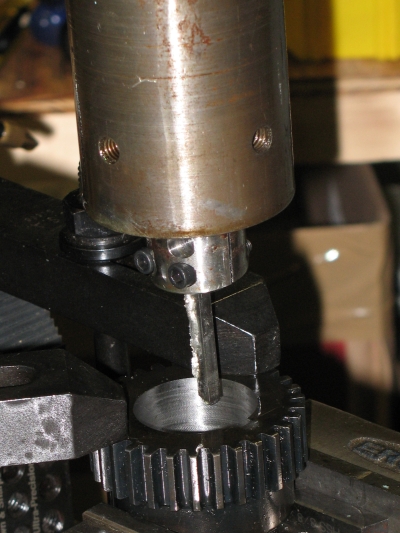
The vise & table combo tends to be springy, so the workholding
should be secure. As can be seen above, my solder job didn't
hold. I later redid it, being more careful with the wetting and it
worked quite well. With a bit of practice with setup and grind I was
able to obtain good cuts without the 1/4" backing tool, particularly in
aluminum.
I found it helpful to adjust the ram gib to pre-load the ram a little
bit. With the gib loose, the ram tended to knock when coming into
contact with the work. The head doesn't nod, but rotates side to
side. I indicated the ram and with the head pointing down and
indicated for vertical, the ram nods .001" or less over about 3". The
prospect of tapering a keyway's depth is interesting, though I don't
know where I'd use it.
The shaper head uses two lubricants, one for the worm gearcase and the
other for the crank and ram.
For the worm, I used Mobil SHC 634 synthetic, available from Enco and
McMaster. This oil is very sticky and the fill hole is small so a
dedicated pump oiler will be helpful.
For the crank and ram I've tried Velocite #10 and Mobil DTE Heavy/Med-
both seem to work fine though the DTE doesn't drain out as quickly.
Overall I'm quite happy with the head. Its nothing like a real
shaper, but being compact and out of the way is helpful- and it makes
keyways a breeze.
12/2006
I made toolholder #2,this one
holds the tool vertically, not angled to relieve the cutting edge.
We'll see if it helps stiffen the 3/16" cutting tool. I think I'll make
the next one hold the tool horizontally with provision for both 3/16"
and 1/4" tooling.
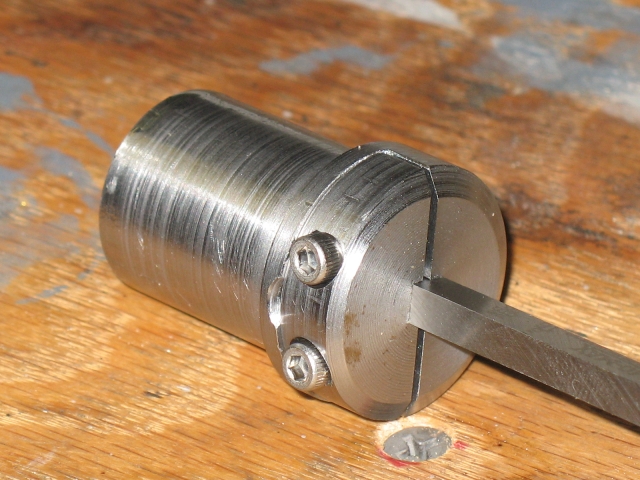
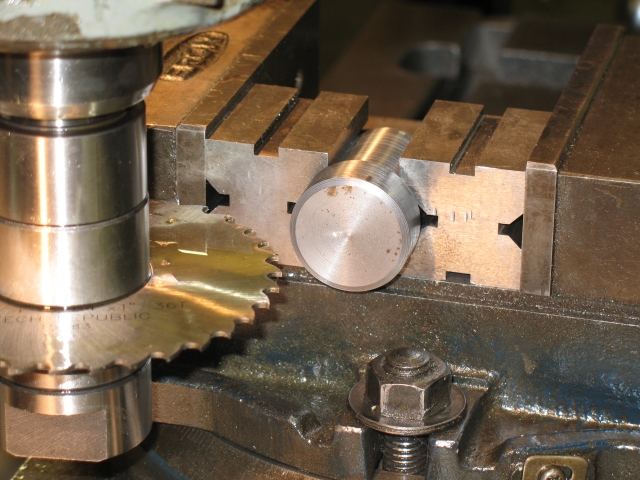
;;; eof